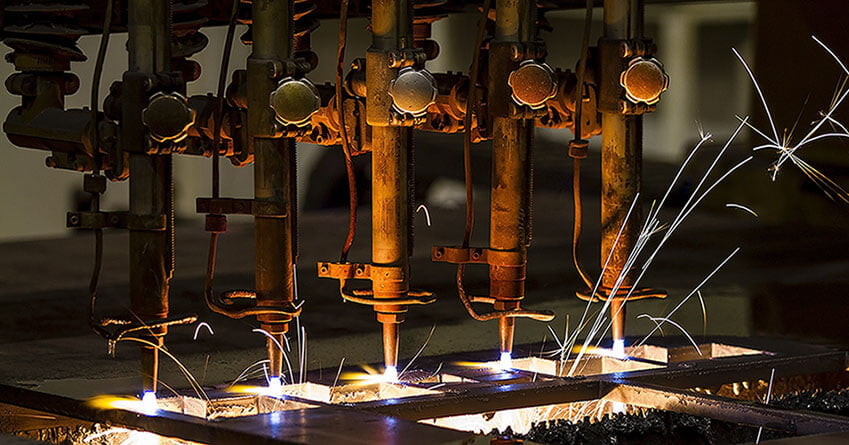
Transformation
continuous
Smart companies seek to continuously evaluate and transform the way they use their assets.
Too often, transformation becomes necessary to maximize resources in response to changing circumstances. In the case of a Quadrillion Partners customer, this change occurred in the form of a plant closure that forced production volumes to different locations and threatened to increase delivery times to critical customers.
Dallas-based consulting firm Quadrillion helped its customer, a global high-tech manufacturer in the middle market, develop a new strategic planning process to make rapid and informed decisions by consolidating global manufacturing sites.
To help with the project, Quadrillion worked with FlexSim to develop a global simulation model that would assist in this critical decision-making.
Managing complexity
The Quadrillion customer has created a complex and productive global manufacturing ecosystem: six factories that produce and ship more than 75 000 SKUs of more than 20 product families. To meet the 600,000 global orders per year, these factories depended on more than 1,000 equipment, dozens of continuous flow manufacturing lines and, in some cases, different "recipes" for similar products in different locations. All this before taking into account these important customer delivery commitments. For the end client, the FlexSim model needed to mimic each facet of the system so that it would be useful, so that realistic scenarios on volume grouping could be executed.
This meant planning a single simulation model linking current orders, customer locations, plants, costs and capabilities. Everything from machine speeds to staff needs, customer logistical routes and the nuances of imports and exports would be considered. Quadrillion collected and prepared an amazing amount of operational data on the system; these data, contained in 22 spreadsheets, can be updated periodically for future simulations and then extracted and processed from solid Excel. by FlexSim.
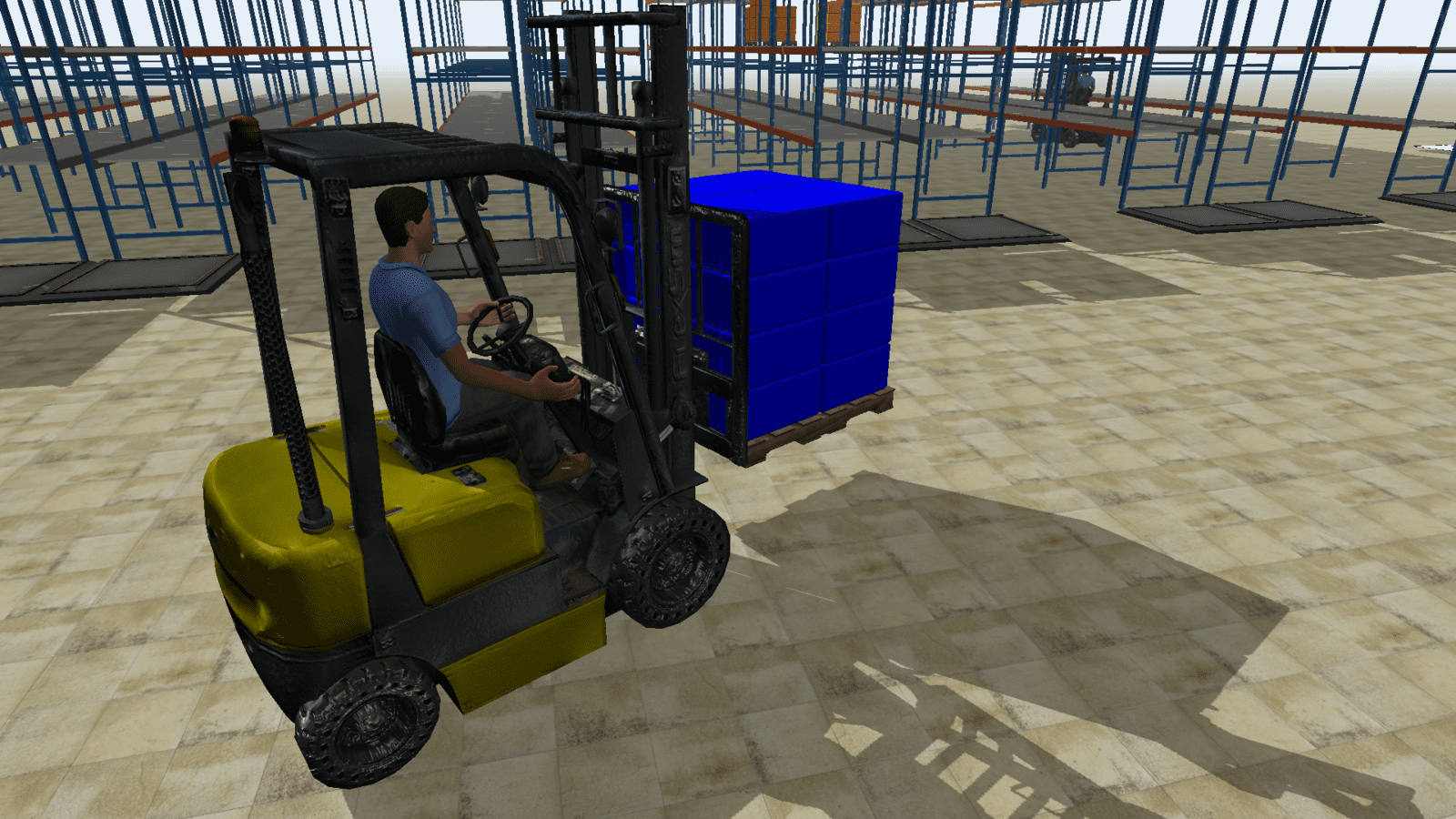
The goal?
Determine options for grouping volumes of product families into different plants worldwide to answer questions such as:
- What products should be produced and where? What products should be produced and where?
- What are the costs and benefits of obtaining products from different regions? What are the costs and benefits of obtaining products from different regions?
- What bottlenecks or capacity problems can arise?
The simulation solution
The simulation model used FlexSim's Process Flow tool, which allows you to model systems using simple steps. This facilitates the understanding and expansion of complex models without losing 3D visual representation. It also adds flexibility and responsiveness to update data across different simulation scenarios.
An example is when the customer wishes to evaluate the expansion of the equipment. By adding machines to an Excel file, model logic is automatically updated, allowing for rapid evaluation of scenarios for urgent decisions.
As delivery time was key, the model included location data developed by Quadrillion, linking each customer's shipping site with each global floor by zip code. These geolocation data made it possible to calculate average delivery times for each product and customer, entered in the FlexSim model. Thus, Quadrillion was able to examine the impact on delivery times by grouping volumes, both at order level and in histograms per product family. The model also showed the balance between speed of delivery and order location.
Results and analysis
The simulation model analysed scenarios such as grouping volumes in regions, plant consolidation and the impact of new labour laws with variable personnel. All critical metrics were included in the output: demand per customer and product, capacity, exchange times, cycle and delivery.
The model also showed when the team reached its limit in a simulation (known as a "bottleneck"), something that is detected only in models that consider real variability and interdependencies. Identified of these bottlenecks can be resolved by improving equipment speed, redistributing demand or replacing parts.
Several immediate results of the model were the decision to increase the combination of volumes throughout the Asia region, the decision to consolidate from six factories to five and an initiative to expand lower-cost imports to higher-cost regions.
A multifunctional and updated model has helped operations and finances make better decisions and better understand their manufacturing process. It is planned to expand it in the future, adding capabilities for faster strategic planning and to meet new manufacturing challenges.
Objectives
Create a simulation model for strategic planning to answer the following questions:
- What products should be produced and where?
- What are the costs and benefits of obtaining products from different regions?
- What bottlenecks or capacity problems can arise?
Results
- Multifunctional model for both operational and financial decision-making.
- Greater grouping of product volumes throughout the Asia region.
- Evidence of an initiative to expand lower-cost imports to higher-cost regions for certain product families.